Heat exchanger tubes made in accordance with ASTM A213 are seamless low alloy steel (Cr-Mo alloy steel) or austenitic stainless steel tubes used for heat transferring in high-temperature and corrosive applications. These tubes are known for their excellent mechanical properties, including strength and resistance to oxidation and corrosion in demanding environments. In a heat exchanger, the tube sheet is a vital component that provides structural support for the tubes, ensuring they remain aligned and secure. It serves as the connection point for the tubes, which are fixed into drilled holes in the tube sheet through welding. Additionally, the tube sheet separates the fluids on either side of the heat exchanger, preventing leakage and maintaining the efficiency of heat transfer. It also plays a role in containing internal pressures, allowing the heat exchanger to operate safely under high-pressure conditions.
The welding processes for attaching heat exchanger tubes to a tube sheet are mainly classified as follows:
- Strength Welding: (1)Principle: Forms a weld with sufficient strength between the heat exchanger tube and the tube sheet, ensuring a solid connection. The weld not only provides sealing but also supports substantial mechanical loads. (2)Characteristics: Offers high welding strength and can withstand high pressure and stress. It requires strict welding process controls and is affected by various factors, making it suitable for high-pressure and high-temperature applications.
- Seal Welding: (1)Principle: Primarily aimed at ensuring the sealing of the connection to prevent medium leakage. Continuous welding is performed between the heat exchanger tube and the tube sheet to create a sealed weld. (2)Characteristics: Focuses on sealing performance with relatively lower welding strength. It is suitable for applications requiring high sealing efficiency but lower mechanical load, such as low-pressure systems.
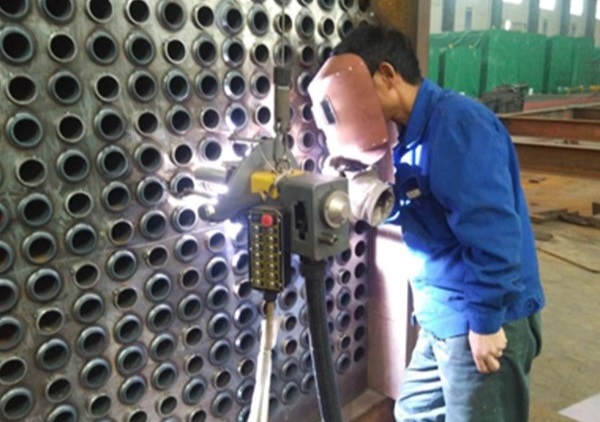
Strength welding for joining ASTM A213 T22 seamless tubes to a heat exchanger.
- Expanding and Welding Combination: (1)Principle: Initially, expansion is performed to create a mechanical bond between the heat exchanger tube and the tube sheet, followed by welding. This approach combines the advantages of expansion and welding to enhance the reliability of the connection. (2) Characteristics: Integrates the sealing performance of expansion with the strength of welding, effectively preventing gap corrosion and vibration loosening. It is suitable for harsh conditions such as high temperature and high pressure.